За результатами спілкування з керівниками аграрних бізнесів, пов’язаних з вирощуванням зернових, елеваторами і зернотрейдінгом, проявляється цікава тенденція: їх інвестори і керівники, від фермерів до агрохолдингів, хочуть прозорості своїх бізнес-процесів і чіткого розуміння, де, що і чому вони втрачають і як це припинити.
Вони розуміють, що повинен бути постійний контроль і облік кількості та якості зерна по всьому виробничому ланцюжку і хочуть такий контроль мати.
Пов’язані ці бажання:
- з боротьбою з «людським фактором» (прямими розкраданнями, різними маніпуляціями з вагою і якістю, помилковими або свідомо невірними діями персоналу);
- бажанням максимально зменшити витрати на всіх етапах роботи;
- необхідністю підвищити прибутковість і ефективність роботи кожного бізнес-процесу у всьому виробничому ланцюжку.
Цілком логічно, що велика сільськогосподарська корпорація, що займається вирощуванням, зберіганням та експортом продукції зацікавлена в обліку вирощеного зерна прямо з поля – з моменту збирання врожаю комбайном і до завантаження його на судно за експортним контрактом. Її керівництво, як і фермер, має бути впевненим, що якщо з бункера комбайна в зерновоз було вивантажено 20 тонн пшениці, то і до елеватора або зернового складу доїхало саме 20 тонн. Щоб було зрозуміло і прозоро, скільки пшениці з цієї партії було засипано в силос на зберігання, а потім відвантажено в вагони, доставлено в порт і завантажено на судно за експортним контрактом.
Ми не говоримо зараз про реальні технологічні втрати та точності ваг – ми говоримо про правильно вибудувану схему роботи по контролю та обліку всієї вирощеної чи придбаної продукції.
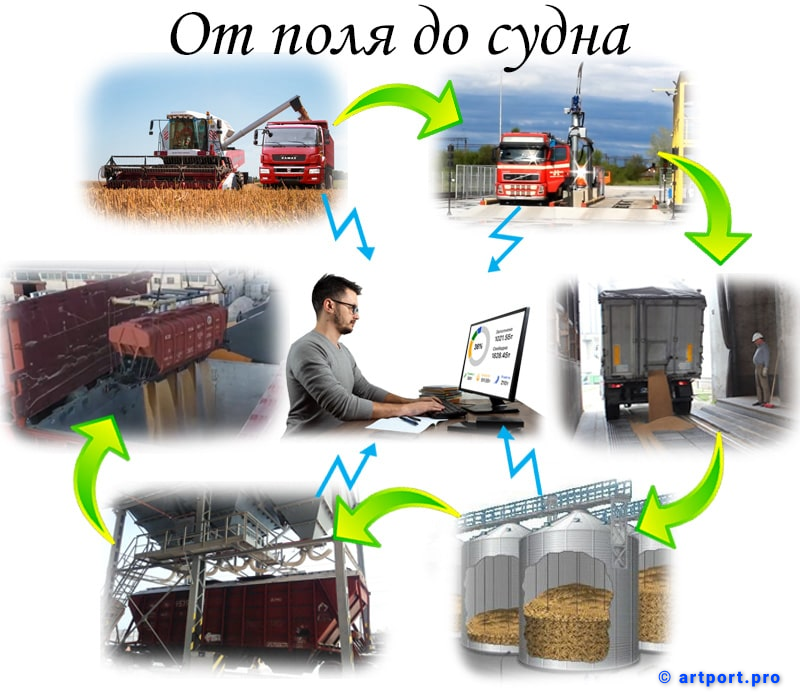
Як це реалізувати на практиці?
Для реалізації такої схеми необхідна «наскрізна» система обліку та управління – «від поля до судна». Побудувати таку АСО цілком можливо і навіть потрібно, особливо для великих агрохолдингів, які мають вертикально інтегрований бізнес від вирощування до експорту.
В рамках цієї статті ми, в найзагальніших рисах, розглянемо етапи всього виробничого ланцюжка і підходи до їх автоматизації.
Про боротьбу з розкраданнями написана маса статей, але одними з основних моментів, спрямованих на боротьбу з цим явищем є:
- постійний і прозорий кількісно-якісний облік продукції на кожному етапі;
- контроль дій персоналу;
- виключення прийняття співробітниками неправомірних і помилкових рішень.
Для цього всі рішення в стандартних ситуаціях повинні прийматися системою управління автоматично, максимально виключаючи вплив людини.
Почнемо з забирання в полі.
Як зрозуміти, скільки тонн комбайн при збиранні завантажив в кузов автомобіля?
Може бути, комусь це здасться дивним, але подібні рішення вже є на нашому ринку.
Невеликі потокові ваги, закріплені на шнеку комбайна, дозволяють заміряти вагу намолоченої продукції при перевантаженні її в зерновоз.
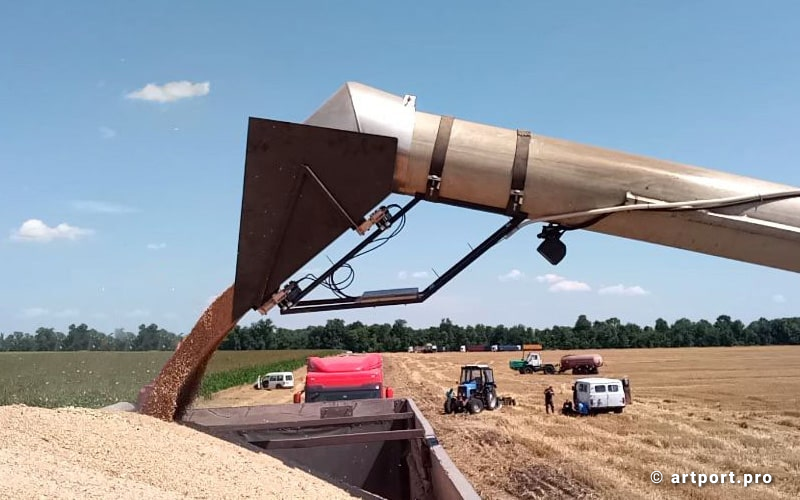
Мобільний додаток для експедиторів або обліковців, які працюють в полі, дає можливість автоматично сформувати та роздрукувати TTH, з якої водій відправляється в рейс. Як мінімум, ці дані можуть бути передані в офіс (бухгалтерію), де на їх основі буде виписана паперова ТТН для водія. А всі необхідні дані передані в облікову систему елеватора, в який везеться це зерно. Співробітники елеватора, зернового термінала (ЗТ) або зернового складу не вводитимуть дані з ТТН вручну, а тільки перевірять їх, що вже саме по собі скорочує час обробки машин і зменшує роль «людського фактора».
Не забуваємо, ще кілька моментів:
- будь-яке вантажне перевезення повинно відбуватися при наявності ТТН (поки в паперовому вигляді), але держава планує обов’язкове використання електронних ТТН (Е-ТТН) для всіх автоперевізників і готуватися до цього потрібно заздалегідь;
- прийняття закону № 1534-ІХ, і повсюдне запровадження контролю за перевантаженням на дорогах і введення великих штрафів за ці порушення так само змушують контролювати вагу зерновозів при завантаженні.
Від поля (зернового складу фермера) до елеватора
Контроль за зерновозами від моменту завантаження на поле або току сільгоспвиробника до елеватора можна здійснювати за допомогою GPS трекерів. Це дозволить контролювати маршрут руху і відсутність позапланових зупинок.
Оптимізація логістики на елеваторі при прийманні автотранспорту поклажодавців
Це відноситься як до питання здачі зерна на зберігання в елеваторі (на склад), так і до його відвантаження з елеватора (складу).
Для збільшення ефективності цього бізнес-процесу потрібно розв’язувати два питання:
- організувати зовнішню логістику – домогтися того, щоб машини поклажодавців під’їжджали до елеватора згідно з електронною чергою, організованої ним самим. Особливо це корисно при здачі декількох культур одночасно;
- зменшити час обслуговування однієї машини.
Управління зовнішньою чергою транспорту на елеваторі (зовнішньою логістикою)
Цей підхід зменшить простої машин поклажодавців і їх витрати на оплату автотранспорту і, як наслідок, збільшить привабливість саме цього елеватора в їхніх очах.
Елеватор же отримає організовану і сплановану роботу, розуміючи яку культуру, хто і коли йому привезе найближчим часом.
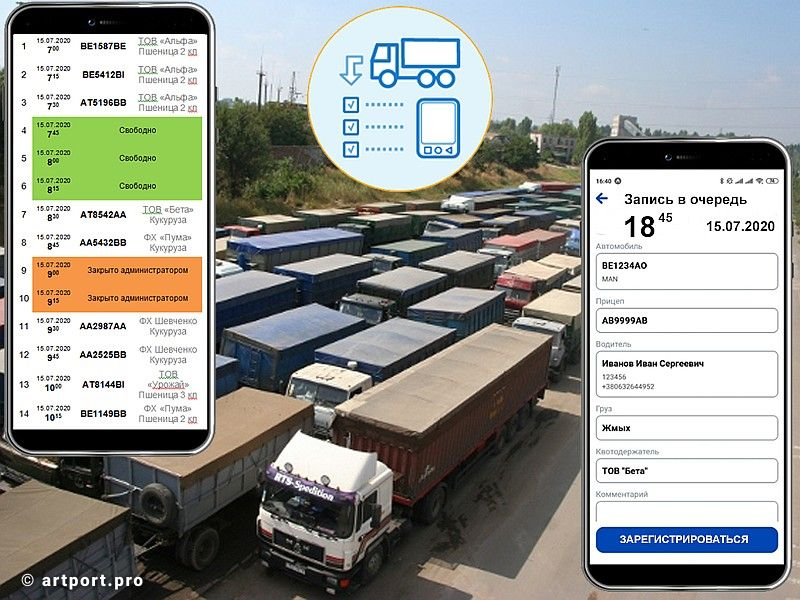
Організація такої черги агрохолдингами на власних елеваторах і тих, що перевозять продукцію своїм же автотранспортом формує плановість роботи, зменшує час простоїв і, як результат, підвищує його ефективність.
Зменшення часу обслуговування однієї машини
Збільшити кількість обслуговуваних машин на елеваторі можна двома шляхами: збільшити кількість точок приймання або/та зменшити час обслуговування однієї машини.
Щодо збільшення точок приймання машин все зрозуміло, а ось про зменшення часу обробки однієї машини трохи поговоримо.
Впровадження систем управління внутрішньою логістикою транспорту, одночасно з обміном інформацією з автоматизованою системою обліку, контролю та управління рухом продукції на елеваторі реально дозволяє зменшити час обслуговування однієї машини до 9-10 хвилин.
Досягається це шляхом:
- чіткої організації всього ланцюжка операцій;
- мінімізації часу введення даних: все, що можна, вводиться автоматично або береться з суміжних систем;
- максимальне виключення участі людини при стандартних умовах проведення операції;
- «навчання» системи управління порядку дій в будь-яких нестандартних ситуаціях. При появі таких ситуацій АСО повинна підказувати оператору його дії та повідомляти про це керівництву;
- створення системи узгодження спірних питань співробітниками елеватора з керівництвом і поклажодавцями. Для цього можуть використовуватися як чат-боти, так і спеціалізовані мобільні додатки, що дозволяють керівництву прийняти рішення, зафіксувати його в АСО, передати підлеглим і проконтролювати його виконання.
Досвід впровадження подібних систем показав, що кількість оброблюваних елеватором зерновозів зросла зі 100 до 150 машин в день, і, в середньому, дозволило збільшити дохід елеватора на 7-15$ за тонну в залежності від оброблюваної культури. А при середній вазі авто у 25 тонн дохід підприємства в піковий день збільшується від 8750$ до 18750$.
А тепер уявіть, що дані по машині (держномер, номер ТТН, культура, водій, вага і т.п.), сформовані в полі при навантаженні з комбайна в кузов або на зерновому складі у фермера, вже внесені в облікову систему елеватора. Робиться це:
Водій знає, що він повинен під’їхати до воріт елеватора, наприклад, в 13:00. Під’їжджає до КПП, отримує заздалегідь підготовлену для нього RFID-мітку (QR- або штрих-код) і, не чекаючи півдня в черзі на майданчику відстою, відразу слідує по бізнес-процесу. Завдання цього ідентифікатора – «стерти ідентичність» машини та всі дані по ній для роботи служб елеватора і виключення «людського фактора».
При цьому оператор КПП не вводить всі дані вручну з паперової ТТН, намагаючись розібратися в чужому почерку, а просто звіряє інформацію з неї з уже введеною в систему.
Далі автоматизована система «веде» цю машину по всьому технологічному ланцюжку, дозволяючи проїзд за допомогою відкриття шлагбаумів або сигналами світлофорів, якими сама та управляє.
Розглянемо цей процес по етапах:
- заїзд на територію елеватора по отриманому ідентифікатору;
- знеособлення взяття проб і виконання лабораторних аналізів. Отримання всіх можливих результатів аналізів з передачею їх в облікову систему. У разі, якщо є розбіжності, які вимагають узгодження з керівництвом елеватора або поклажодавцем, існує можливість їх узгодження в чат-ботах або в мобільному додатку «Арт:Директор зернового термінала»;
- зважування брутто. Цей процес повністю автоматизований і захищений від втручання в результати зважування. Система контролює правильність постановки автомобіля і причепа на ваги, звіряє номерні знаки на автомобілі та автоматично передає результати зважування в АСО ТП;
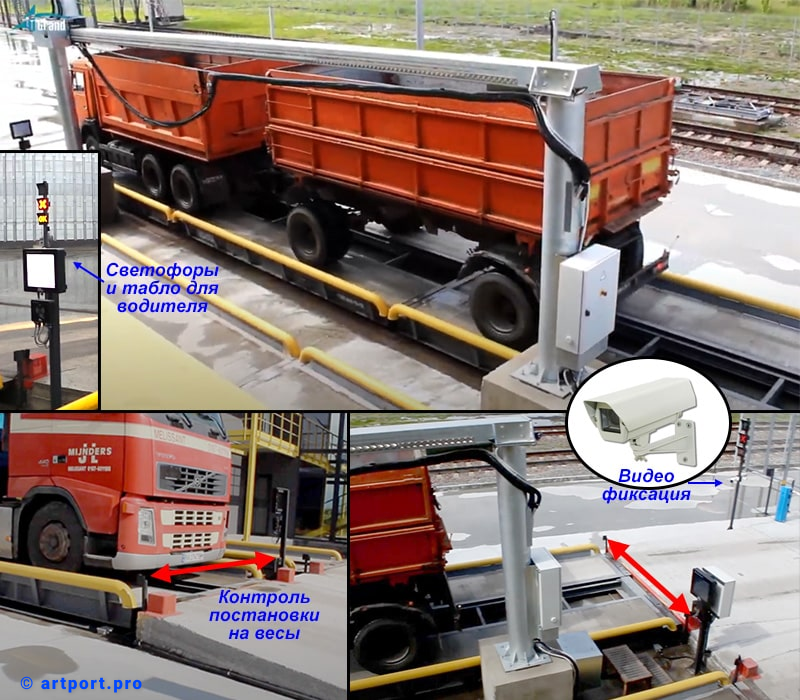
- за результатами лабораторних аналізів АСО ТП автоматично визначить, на яку завальну яму потрібно поставити машину. Водієві буде видано про це відповідне повідомлення на електронному табло і система пропустить його на певну завальну яму. При цьому АСО ТП автоматично вибере необхідний маршрут прямування зерна по елеватору в залежності від результатів аналізів. Такий крок дозволить уникнути пересортування та інших негативних наслідків. Важливо, що АСО ТП запускає максимально короткі або менш енергомісткі маршрути. І тут ефективність досягається внаслідок економії енергоресурсів;
- зважування нетто. При цьому, для виключення зловживань, вага машини порівнюється з минулими результатами зважувань і, в разі різких розбіжностей (зазвичай це 300-400 кг, що є еквівалентом повної ваги палива в автомобілі), видається сигнал про нестандартну ситуацію. Така різниця говорить про можливу махінацію;
- після виїзду через КПП водій отримує завірені паперові документи.
Причому, при будь-якій дії в системі відбувається автоматичний запис часу здійснення операції, фото або відеофіксація цієї події. На вагах і в лабораторії часто використовують модулі розпізнавання номерних знаків для порівняння номерів авто з тими номерами, що прив’язані до ідентифікатора (ТТН).
Автоматизація процесу приймання значно скорочує витрачений час, прискорює зважування, лабораторний аналіз, знижує вплив людського фактора і, відповідно, зменшує кількість помилок. Скорочуються витрати на утримання вагарів, а на деяких підприємствах і пости охорони, а це 250-300 тис. грн в рік за один пост.
Управління технологічними процесами на елеваторі
Окремо поговоримо про автоматизацію роботи, пов’язану з технологічними процесами (АСО ТП) підготовки та зберігання зерна.
Автоматизація цих процесів дуже важлива. Її завдання полягає в правильному і швидкому ухваленні рішення про направлення чергової партії на очищення, сушіння і т.д. АСО ТП приймає рішення тільки виходячи з об’єктивних даних – результатів лабораторних аналізів, виключаючи людський фактор і управлінські помилки.
Наприклад, вологість зерна визначена як та, що перевищує норматив. Це значення автоматично потрапляє в АСО ТП, яка сама приймає рішення і відправляє його на сушку. Співробітник не бере ніякої участі в цьому процесі, тому що воно очевидно і не потребує «людину». Автомобіль під’їжджає до бункеровки, а там вже всі транспортери «знають», що зерно з цієї машини відправляється на сушку. Після цього, залікова вага зерна перераховується і в облікову систему «йде» вже остаточна вага і якість. Таким чином, маніпуляції з вагою і якістю зерна на цьому етапі технологічного процесу виключені.
Так само АСО ТП повинна враховувати енергетичні витрати елеватора на виконання кожного етапу технологічного ланцюжка.
Наприклад, знаючи, скільки зерна і з якою вологістю зайшло в сушку і вийшло з неї, а також витрати енергії на цей процес можна моніторити ефективність її роботи і шукати шляхи підвищення енергоефективності конкретного технологічного процесу.
Аналогічно і по всім іншим техпроцесам, пов’язаних з підготовкою і зберіганням зернових на елеваторі.
Облік і контроль зерна на етапі від елеватора до судна
Що стосується обліку при зберіганні і підробітку зерна, то це досить тривіальний процес, відпрацьований у багатьох вже існуючих АСО і зупинятися на ньому ми не будемо.
При перевезеннях зерна з лінійних елеваторів на портові зернові термінали в більшості випадків використовується залізничний транспорт.
Сьогодні існують готові апаратно-програмні модулі, що дозволяють автоматично вести облік навантаження зерна в вагони.
Хотілося б трохи поговорити про питання швидкої та правильної підготовки документів і прискорення обслуговування вагонів при прийманні/передачі їх УЗ для перевезення і про контроль дислокації в русі та подачі хоперів на зерновий термінал точно в строк.
Співробітники, що готують вагони до відправки (завантаження, зважування, пломбування і т.п.), не дивлячись на те, що працюють «в полі», повинні мати засоби доступу до облікової системи елеватора або зернового термінала. Оптимальним для них знову ж стає використання спеціалізованих мобільних додатків в смартфоні. За допомогою таких програм можна автоматизувати роботу співробітників у власній АСО і роботу з «Укрзалізницею» на всіх етапах: навантаження, перевезення і контроль дислокації вагонів, вивантаження, підготовку всіх необхідних документів для УЗ.
Швидка обробка вагонів (навантаження, пломбування) і підготовка необхідних документів для УЗ, особливо це стосується великих компаній, що перевозять зерно складами, дозволяє економити на оплаті їх оренди. Підприємство платить УЗ за реальний час використання вагонів, а не за час простою, коли вагони стоять на станції й чекають поки співробітники, що відповідають за їх огляд, перевірку пломб і т.д. проведуть огляд, повернуться в офіс і підготують всі документи на склад. Мобільний додаток дозволяє все робити прямо на станції в момент огляду вагонів, тим самим заощаджуючи час і гроші.
Існує ще й спеціалізований сервіс УЗ «Direct_UZ», що допомагає організувати доставлення складів із зерном в порт прямо під швартування судна, уникаючи зайвих витрат на зберігання і перевалку зерна спочатку в зерновий термінал, а потім на судно.
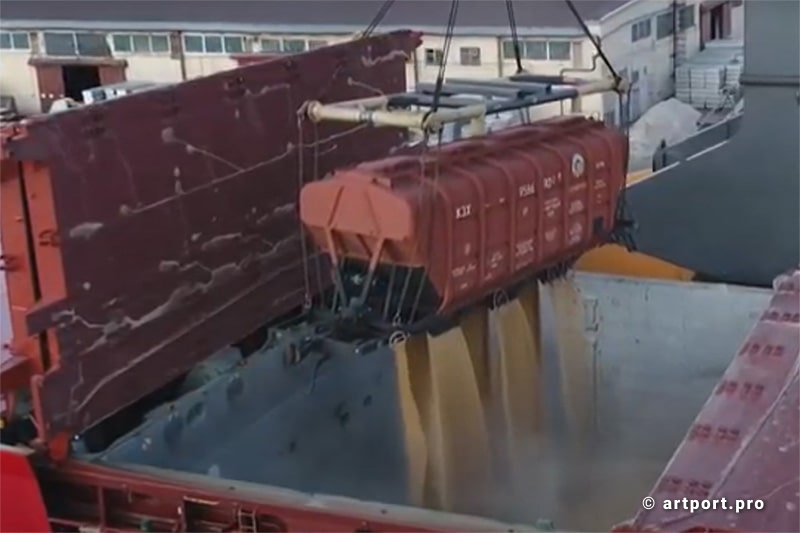
Навантаження на судно
Процес вантаження зерна на судно можна розділити на три частини:
- Фізично перевантажити зерно, вже накопичене на зерновому терміналі на судно.
- Організація роботи в разі, якщо потрібне пряме перевантаження з вагонів і автомобільного транспорту в трюм.
- Підготовка та оформлення всіх документів по цій угоді (про якість зерна, дозвільних, митних, податкових тощо)
На сьогоднішній день так само існують програмно-апаратні автоматизовані системи, що дозволяють вести облік навантаженого зерна по трюмах, згідно плану навантаження, і детально зупинятися на описі їх роботи ми не будемо.
Як і в випадку із залізничним транспортом не всі співробітники портового ЗТ працюють в офісі. Частина з них зайнята в роботах на території. Яскравим прикладом є контроль вивантаження автотранспорту в порту на судно. Робота тальмана не прив’язана до стаціонарного робочого місця, а завдання оперативної реєстрації часу і місця вивантаження актуальна та обов’язкова. Контроль за рухом транспорту від складу до судна може виконуватися спеціалізованим мобільним додатком «Арт:Тальман ЗТ».
Про що хочеться сказати наостанок
Автоматизації системи обліку та управління «рухом» сільськогосподарської продукції від бункера комбайна до трюму на судні вже стає аж ніяк не фантастикою, а нагальною необхідністю в сучасному аграрному бізнесі.
Звичайно, не весь цей ланцюжок потрібен всім учасникам ринку.
Великим аграрним корпораціям, у яких є всі етапи, від вирощування до експортних контрактів, потрібна така система в повному обсязі та навіть з набагато більш широким функціоналом, що включає управління фінансовими потоками, транспортом, документами, персоналом, аналітичною підсистемою і т.д. Їм необхідний повний облік і контроль на всіх етапах виробничого ланцюжка.
Для фермера, який вирощує і везе свою продукцію на елеватор, цілком може бути досить контролю від комбайна до силосу на елеваторі. Його завдання не допустити будь-яких втрат при перевезеннях з поля і зберіганні на елеваторі або власному зерноскладі.
Для зернотрейдера, що купує зерно у виробника і продає його експортеру потрібна система ведення та обліку операцій та придбаної продукції на етапах від складу сільгоспвиробника до моменту завантаження в елеватор, портовий ЗТ, зазначений покупцем, або відразу на судно.
Існуючі сьогодні технічні засоби автоматизації та програмні модулі дозволяють виконувати автоматизацію і контроль на всіх етапах роботи. Однак, побудувати таку «наскрізну» систему насправді не так просто, як здається на перший погляд.
На ринку є різні модулі, що «відповідають» за окремі описані вище ділянки. Але практично всі вони розроблені різними розробниками і не становлять цілісної системи. При розробці подібних АСО, потрібно враховувати масу нюансів конкретного замовника, особливостей використовуваного обладнання, технологічних, управлінських та облікових процесів, прийнятих у нього. Логічно будувати такі системи з одним системним інтегратором, який може об’єднати всі модулі в єдину працюючу систему.
Досвід спільної роботи ТОВ «Арт Порт» говорить про те, що будувати і впроваджувати такі системи можливо і цілком реально.
Питання тільки в тому, що той, хто перший запровадить автоматизацію хоча б на більшості етапів, той явно отримає значні конкурентні переваги в боротьбі за своє місце на ринку, особливо з урахуванням заходу до нас іноземних агрохолдингів, які мають подібні системи.